Electronics Technical Hub > Technical Reference Online > Huge robots handling thin glass
Huge robots handling thin glass
Huge transport robot developed to handle glass as thin as paper
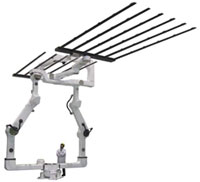
Yaskawa Electric Corp., the largest manufacturer of industry robots in Japan, produces a wide variety of robots including coating robots for automotive industry and transport robots for semiconductor wafers and LCD mother-glasses. A newly developed transport robot designed for the tenth generation LCD panel production line has been delivered to a major LCD manufacturer, and is quite different from conventional designs. Yaskawa perfectly integrates the company wisdom through a horizontal cooperation beyond internal departments to develop the new robot.
Developing a transport robot for large LCD (liquid crystal display) displays has a lot of new challenges that conventional industrial robots did not have. Yaskawa Electric announced the transport robot for the tenth generation (10G) LCD panel at end of November 2007, and started to sell it in December 2007.
The MOTOMAN-CDL3000D was awarded with the President Award of the Japan Machinery Federation of eight excellent awards in the Robot Award 2008 held by METI (Ministry of Economy, Trade and Industry) in December 2008.
A mother-glass for the 10G LCD panel measures 2.85m long by 3.05m wide with only 0.7mm thin. Why is it so large? This is because the 10G glass corresponds to 15 LCD panels for 42-inch LCD TV while a conventional 8G glass corresponds to only 8 LCD panels. Productivity may be almost doubled, leading to lower production cost.
Conveying thinnest glass substrate like paper
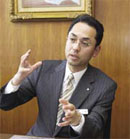
The robot carries very thin and huge glasses from equipment to equipment or from equipment to cassette and vice versa. You can easily imagine how the glass is so huge and thin compared with a usual A4-sized paper with 0.1mm thickness. A mother glass is 134 times larger than an A4-sized paper measuring 210mm by 297mm, and only 7 times thicker. This means the mother-glass seems to be thinner than a paper. The robot conveys very fragile paper-like glasses. “It seems like fluid rather than a glass substrate," said Masahiro Ookura, General Manager, FPD Robotics Business Division of the company.
Handling it requires a tightly-controlled technology. Furthermore the robot must have a wide stroke of 4.5m height upward and downward, to put LCD glasses in and out to thermal processing equipment. LCD manufacturing equipment must also increase a throughput of a number of processed glasses per hour, meaning that the robot requires higher speed operation. The height of the robot must not be too high so that it can be carried into LCD factories. And the size of the robot in a sleep state should be relatively small to carry it onto a truck. Furthermore, dust should not be generated as it operates in a clean room of LCD factories.
The new robot overcame these challenges, and was delivered to a major LCD panel manufacturer
Difficult to achieve it with evolutional technologies
Through the MOTOMAN-CDL3000D development, engineers realize that it would be difficult to achieve the new robot with evolutional robotic technologies. In a conventional robot with a linear up/down scheme, the range of up/down stroke requires 4.5m, and it was too long to convey into a factory. So, the main pillars with 4.5m height had to be cut to two portions, and re-assembled at their customer’s factory. Therefore, LCD panel manufacturers had to schedule the re-assembly operation. The procedure requires a very tight minute by minute schedule. LCD panel manufacturers have accepted the linear pillar robot, according to Ookura. The linear pillar scheme has a structure that needs filters to absorb and exhaust air, just like an inflator of a bike, leading to periodical exchange of the filters.
On the other hand, an elbow-bent scheme robot requires over 2.25m long in each elbow for a stroke of 4.5m, and it might be too long horizontally in a bent state to adopt the scheme in a production line. It is unacceptable. Also a robot required a small footprint. The only advantage is that it is maintenance-free, since there is no mechanism needed in absorbing and exhausting air.
Gathering wisdom from LCD and Automobile Teams
Both schemes had advantages and disadvantages, and it was impossible to just extend the mechanism for larger glass panels. So, the new project of the robotic development integrates two wisdoms of LCD development and automotive line development teams. The LCD team knows customer’s requirements very well, while the automotive team has other know-how from automotive requirements. The different industry group meeting makes sense of educing technical ideas, according to Ookura.
At the initial stage, both teams discussed periodically to share technical information once a week. It took three to five months to complete an architecture design. However, once a target design completes, it took only three months to produce a prototype.
2.5m Height Machine Achieves 4.5m up/down Stroke
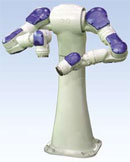
The newly-developed “up/down double-link pillar type" consists of double elbows to maneuver up/down operation. The double-elbow system has three arms. The robot has a pair of the double elbow structure on both sides. The pair of double elbow systems supports a wide and thin mother-glass. Two driving motors are installed in a double-elbow system, which means there are four motors in the robot. Furthermore, four motors operate cooperatively, leading to the smooth operation in not only vertical operation but also horizontal operation. In a horizontal operation, Yaskawa added a twist operation.
In the lower elbow, the arms operate in 180 degrees, quite different from conventional methods. Conventional elbow-bent scheme was able to operate only up to 90 degrees.
The newly developed robot transports a glass substrate with 3m by 3m at a horizontal speed of 4m per second, along with a high accuracy of less than 3mm fluctuation at the tip portion of the glass. In addition, it can correct a shift less than 50mm horizontally.
Yaskawa plans to expand the robot product series to the lower-end LCD panel factories of 7G and 8G designs. The newly developed machine will be applied not only to LCD factories but also thin-film solar cell factories.